Finished Kurume Kasuri fabric measures 37 to 38 cm across and 12 m in length. The fabric goes through roughly 30 processes before it is finished, and almost all of these are still done by hand.
1.Pattern design
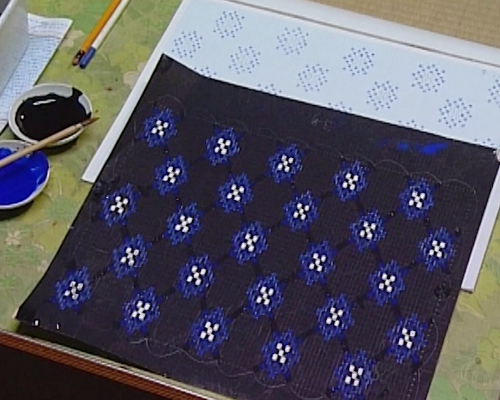
A design suitable for Kurume Kasuri is devised by utilizing traditional patterns while incorporating the individuality of the pattern maker.
2.Pattern sheet
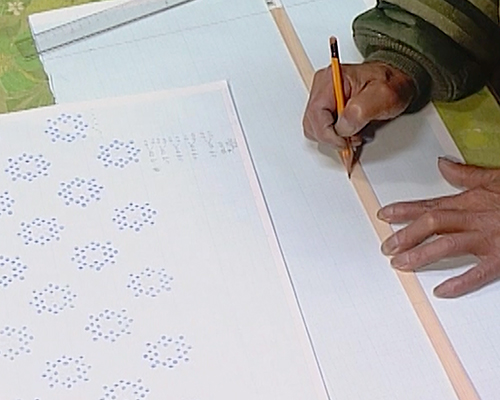
Based on the design, the distribution of warp and weft yarn is calculated and sketched on a pattern sheet. Next, the design is re-sketched in consideration of how much the weft will shrink. This is called shitae.
3.Thread marking (Only for hand-woven fabric)
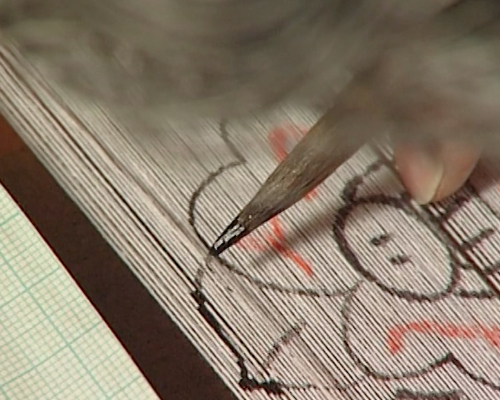
This step forms the basis for weaving the weft. Taut white pieces of thread called seed yarn are carefully marked with ink according to the shitae. All the parts that will be tied and resist dyed to become the kasuri pattern must be marked.
4.Thread adjustment (Warp preparation)
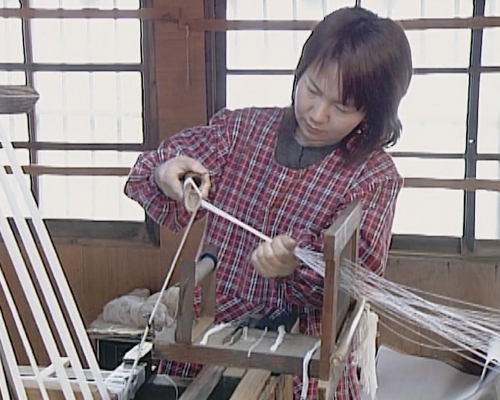
Based on the pattern, the numbers of kasuri-ito (resist-dyed yarn) and ji-ito (solid dyed yarn), and the warp threads are adjusted while taking into account the expansion and shrinkage of the threads.
5.Thread adjustment (Weft)
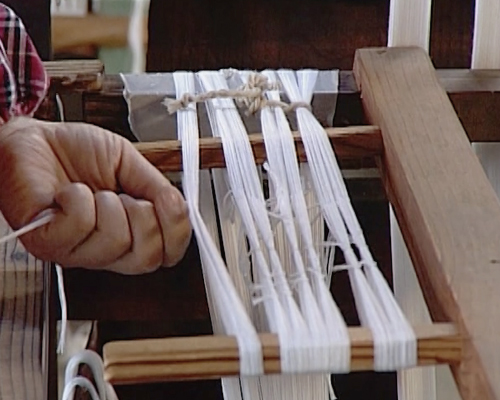
The yarn is boiled in a sodium hydroxide solution to strengthen it and remove impurities. After bleaching and starching, the yarn is dried to prevent fraying and fluffing.
6.Cleaning, bleaching and starching
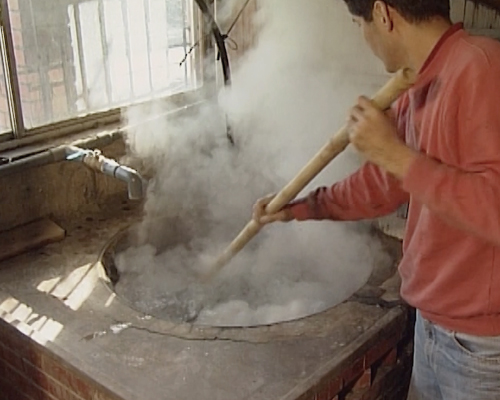
The yarn is boiled in a sodium hydroxide solution to strengthen it and remove impurities. After bleaching and starching, the yarn is dried to prevent fraying and fluffing.
7.Kukuri (Tying off)
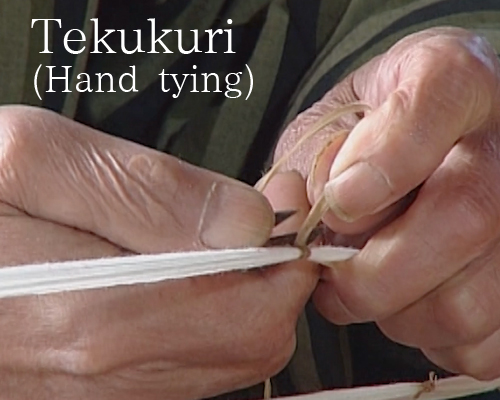
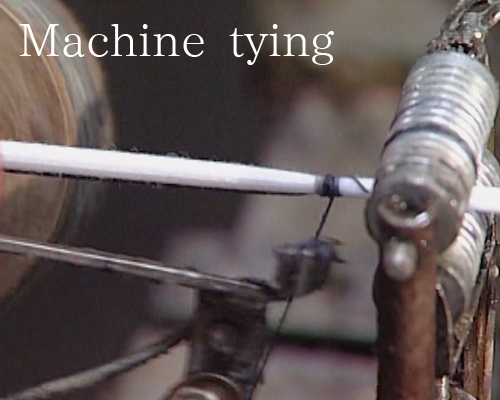
The parts of the warp and weft that will become the pattern are tied off to prepare for resist dyeing. This technique forms the basis of the kasuri pattern, and this is an important step that affects the finished work.
Tekukuri (Hand tying)
The thread is tightly tied off using pieces of hemp thread made by steaming and stripping hemp plant stems. Skill is required to ensure the knots do not unravel during the dyeing process but can be easily untied afterward.
Machine tying
This technique uses a machine to tie off yarn.
Orijime
Another weaving method for making kasuri thread (a resist-dye method by weaving once before dyeing). This technique allows the weaver to efficiently create intricate patterns that cannot be made with the kukuri method.
8.Dyeing
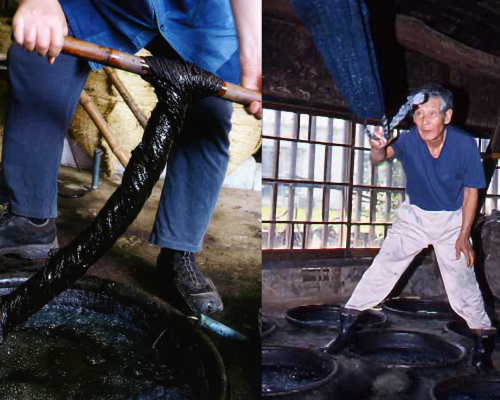
High-quality fermented dried indigo from Tokushima Prefecture is used for dyeing. After it fully ferments for 2~3 weeks, it is ready to be used for dyeing. Yarn is soaked in a vat of indigo buried in soil, after which it is soaked, wrung out and hit against the ground for a combination of about 50~60 times. Dyeing is a multi-step process, starting with paler pigments and working up to darker ones.
9.Washing and untying
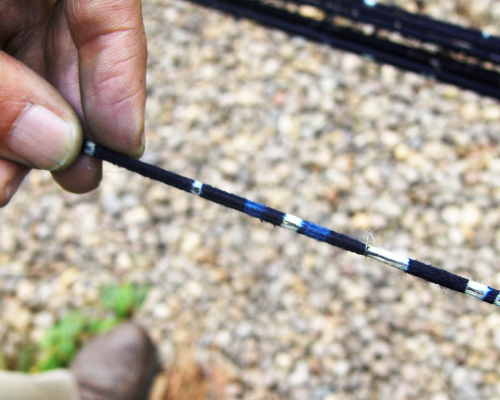
Yarn is soaked overnight in warm water to remove any impurities and excess indigo left over after the dyeing process. The washed yarn is stretched out, but if it is left to dry completely, the white sections will lose their vibrant hue, so the hemp yarn must be untied quickly. After untying the hemp yarn, the thread is washed in water.
10.Starching and drying
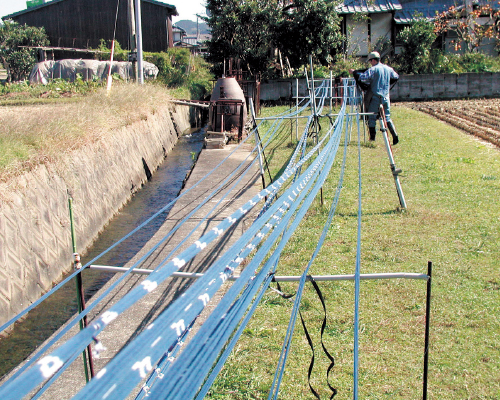
A thin layer of starch is applied to the weft yarn, and it is left to dry it in the sun. This prevents fluffing and increases thread strength. After this step, the processes for the warp and weft differ.
11.Warp Splitting and Pattern Matching
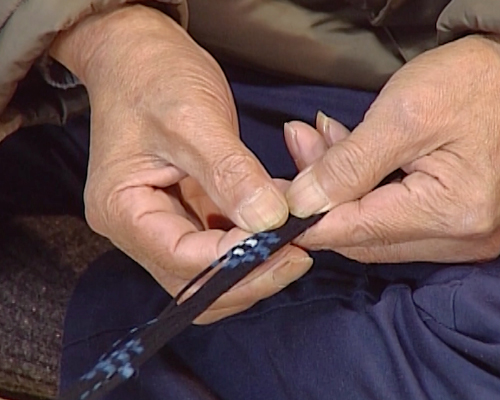
The thread that was folded in four and tied up is now split and stretched, and each group of yarn is tied together with thread to match the pattern.
12.Starching and drying
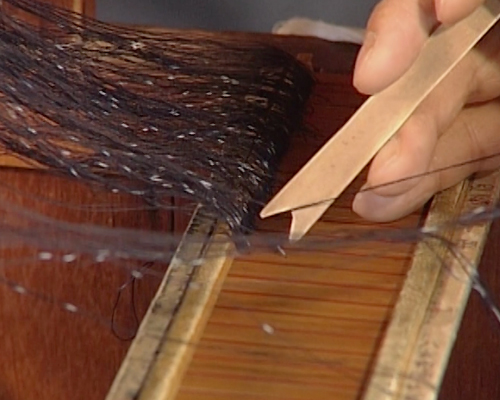
The warp yarn is thoroughly coated in wheat starch paste, the excess water is removed and the yarn is dried quickly while the paste is still warm. This prevents fluffing and fraying and makes the yarn easier to weave.
13.Thread merging and reed drawing
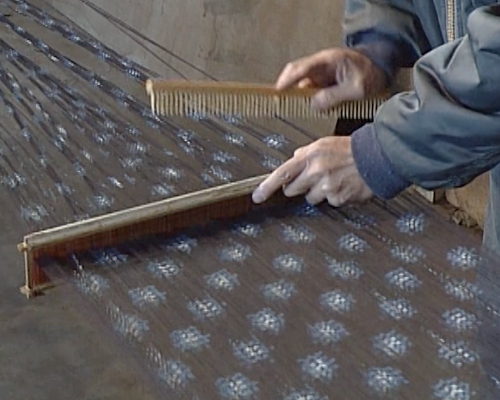
In order to match the kasuri pattern to the width of the fabric, the kasuri yarn and solid colored yarn are merged and arranged according to the number of threads calculated on the pattern sheet. The arranged warp threads are then passed one by one through a reed.
14.Warp winding
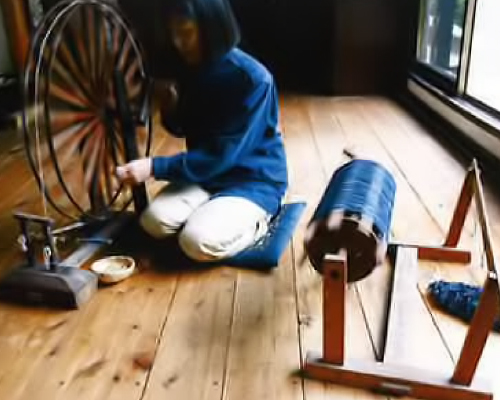
Based on the pattern, the warp yarns are wound around a warp beam. The yarn is pulled tight and combed, and heavy stones are used to maintain tension throughout the weaving process.
15.Weft winding
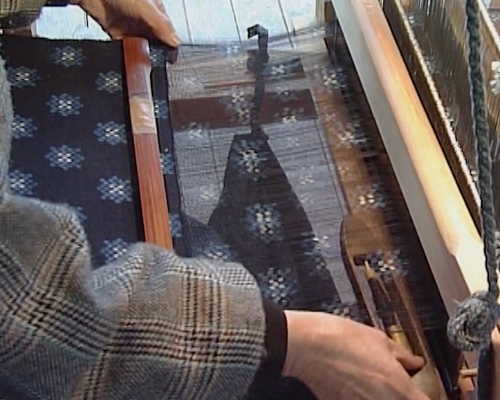
For hand weaving, a spinning wheel is used to wind the weft yarn one by one around a bamboo tube that will be put in the shuttle. For machine weaving, the tongs are arranged on a flat plate and the thread is wound up while keeping the pattern in alignment.
16.Weaving
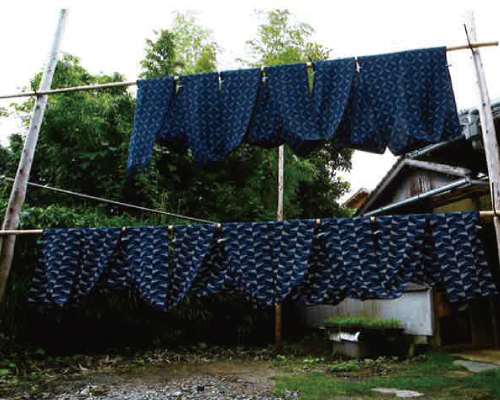
A high level of skill is required for both hand weaving and machine weaving. For hand weaving, an end-feed shuttle is used and the weaver carefully weaves the threads while keeping the patterns in alignment. The height of the heddle (the part of the loom that separates the warp to let the shuttle through), the weaver’s footwork, and the intensity with which the weaver strikes the reed all affect the quality of the finished product. Machine woven fabrics are made using a carefully maintained 100-year-old machine loom, and weavers can weave about 20 meters of fabric on a typical day.
17.Shrinking and Drying
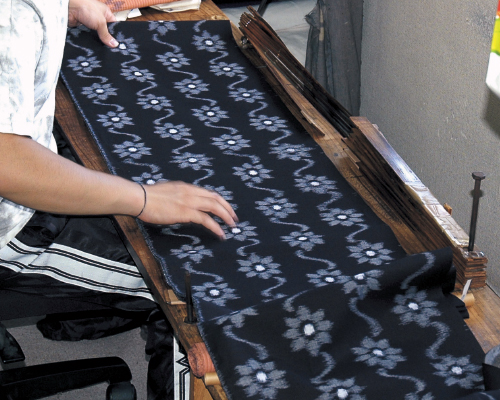
The final product is steamed, which causes it to shrink and leaves it with a supple finish. After it is washed in water, it is hung on a pole to dry in the shade.
18.Folding
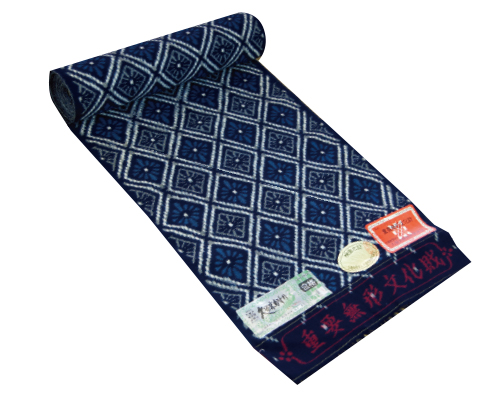
The textile is placed on a measuring table called a shakudai, the puffs are removed with scissors, and it is cut to the specified length while checking the width and finish. Finally, the finished fabric is folded in four.
19.Inspection
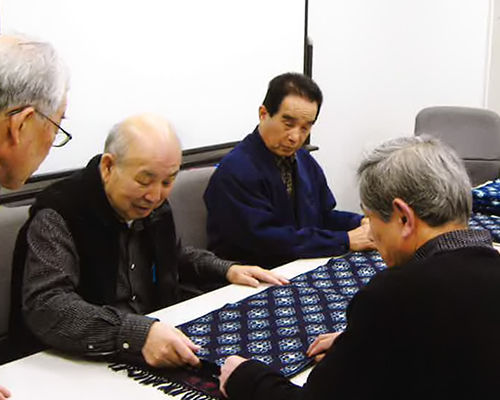
The finished product is inspected by the Kurume Kasuri Association, and the producer attaches a certificate of assurance on the end of the fabric.